
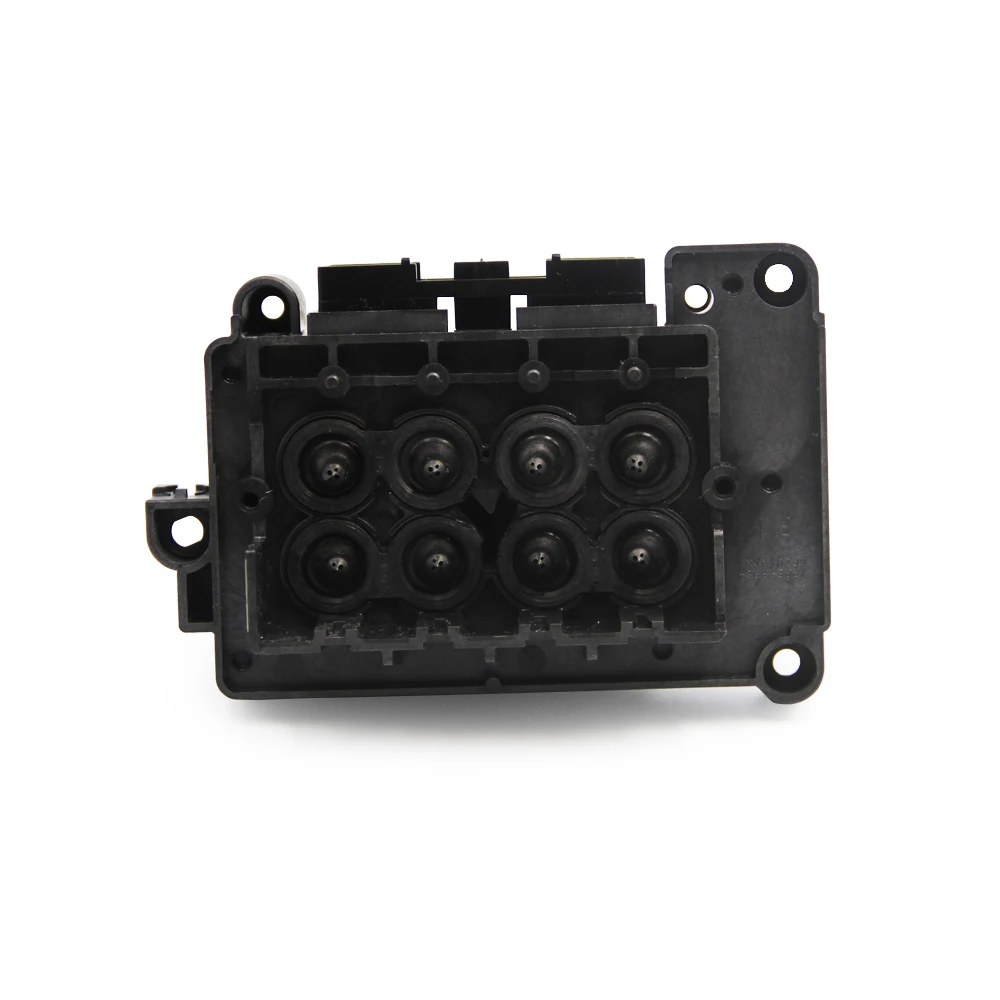
It wasn’t until I made my first plate from a paper stencil that I understood the true benefits of the approach. I realized that afternoon that I could dispense with the scanner, computer, and craft cutter if I picked up an X-ACTO knife and cut the paper by hand.
#Epson 3880 printer print on velum full#
Nikki specializes in papercut and the gallery was full of these beautiful, intricate works that looked just like prints, but were each cut from a single sheet of black paper. My breakthrough came while touring the Nikki McClure exhibit at the Bellevue Arts Museum. The plates were beautiful, but I felt like a technician and the process was stressful and riddled with opportunities for failure at every step. While I was thrilled to be able to make these plates, I was a little disappointed because the process was complex and expensive and required lots of time with my mind outside of the artistic space as I scanned my artwork, adjusted it in Photoshop, converted edges to vectors in Illustrator, cut the vinyl with a Silhouette craft cutting machine, and transferred the vinyl to glass using special adhesive transfer paper. These negatives worked because the flat nature of the glass ensured perfect contact with the plate during exposure and the opaque black vinyl on the clear glass gave me super-high contrast. For weeks I had been trying to develop a process that would allow me to make really crisp and clean relief plates with fine details. After many weeks of experimentation, I had managed to make a couple of excellent plates from negatives made out of glass covered with black adhesive vinyl. I found a really great way to make SolarPlate relief plates using paper stencils. It sounds like a lot, but after a while you get in a rhythm and things go smoothly.
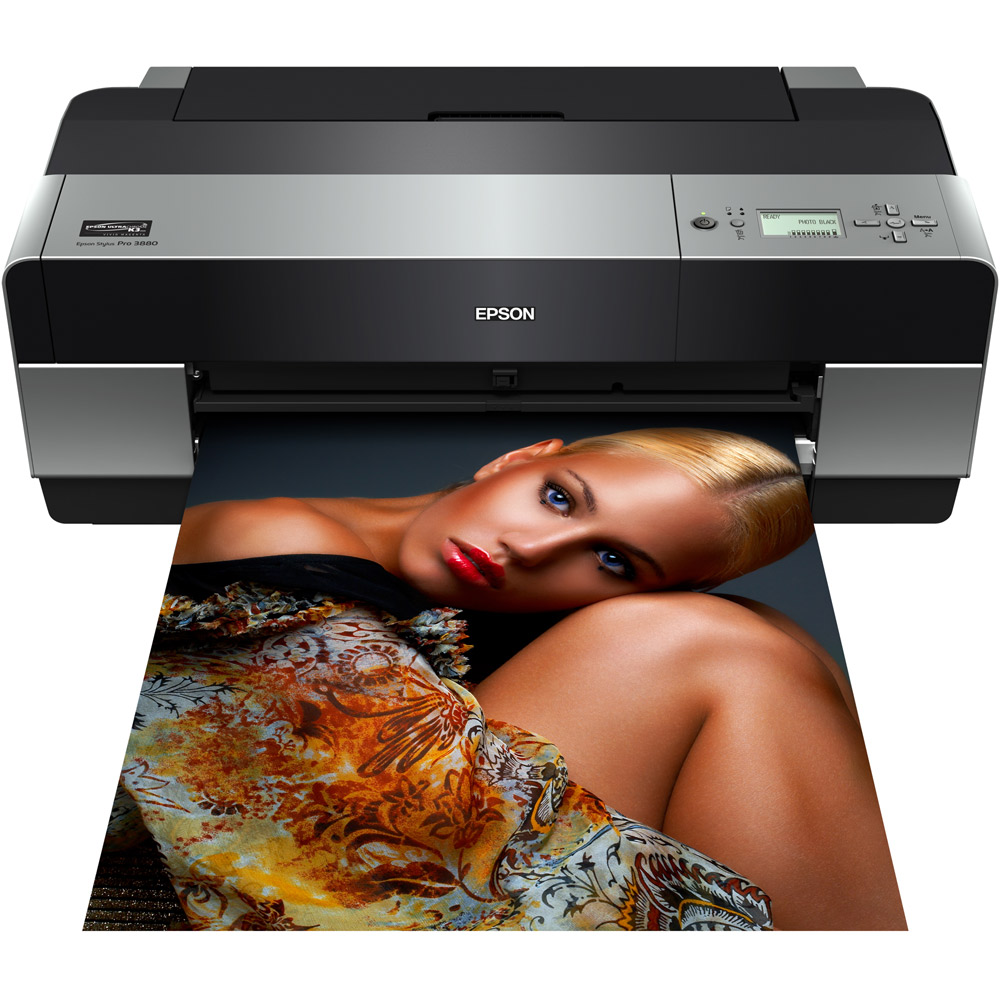
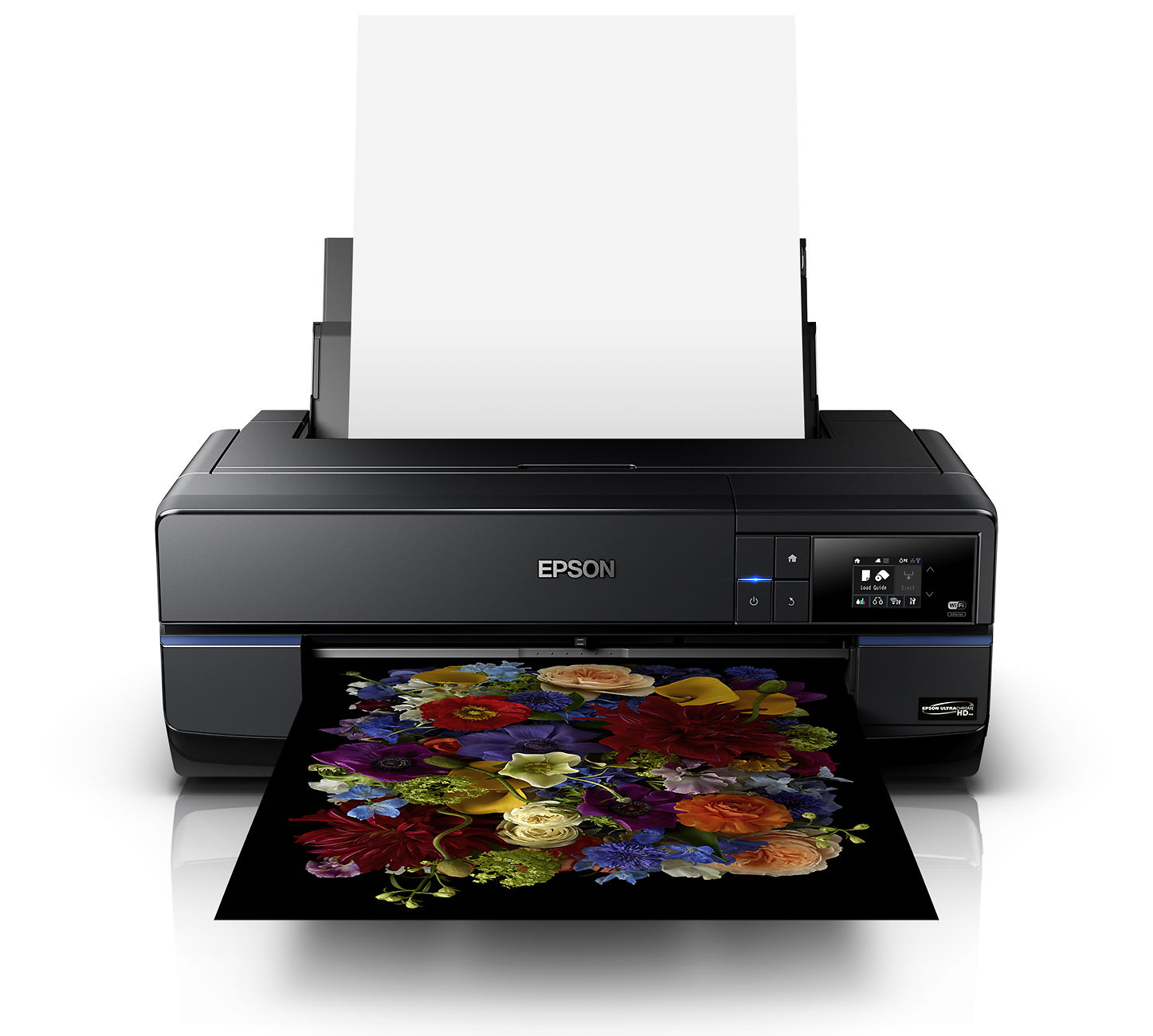
Wipe off the printing press bed which may have ink from the previous plate.Wipe off any ink that may have made it to the back side of the plate.Wipe ink off the sides of the plate from the bottom.Remove this ink with paper towels and newsprint tortillons. Carefully inspect the plate for drops or splotches of ink in the whites.Carefully inspect the plate for any dust or hair that may have fallen in the ink.Carefully inspect the plate for areas that don’t have enough ink.Roll the ink carefully onto the plate in multiple passes and multiple directions.Make sure the roller doesn’t have too much ink.It really helps to get a good process that you follow every time to reduce the chance of mistakes. It turns out there are a million ways to mess up a print. The total includes a number of redos after boo boos. For each print I made a test print on newsprint, followed by a proof on Masa, and then a good print on Hosho. Overall I pulled about 25 prints over the course of the evening. This weekend I finally had a chance to print my new relief plates.
